Thermal management of electronics is essential to a product’s dependability, efficiency, and lifespan. Incorporating thermal analysis early in the design process is not just best practice, but necessary for engineers to deliver high-quality products in the ever-changing landscape of electronics design. Modern electronics are increasingly more complex and compact, and using engineering simulation allows engineers to test their design under real-word conditions in a virtual space to reduce physical testing and redesign.
Overheating can lead to performance degradation, accelerated aging, or catastrophic failures. Identifying excessive heat buildup early in the design process can reduce costs and accelerate product development by helping engineers identify hot spots so they can implement effective cooling strategies. Through thermal analysis, engineers can also understand the thermal interaction between components in an electronics enclosure and adjust the spatial arrangement to ensure long-term reliability and mitigate design risks which will streamline the design process.
Electro-Thermal Analysis of PCB
The modern PCB often contains complex circuitry with numerous components that must fit into a small space. The PCB design process must accommodate for this complexity while balancing the signal integrity, power distribution, thermal management, and manufacturability of the design. Ansys has several electronics and thermal simulation tools that are often used in concert to make informed decisions and mitigate risk for PCB design. DRD Technology has also published a webinar on some of these workflows on their website.
In Ansys Electronics Desktop (AEDT), a DCIR analysis is a valuable tool for PCB design that enables informed decision making around the application requirements. It is often used to understand voltage drops that can affect the performance of active components, identify regions of high current density that can cause hot spots, optimize the placement and thickness of traces, and other design issues. Detecting these early in the design process saves time and money associated with physical prototyping and testing. The losses measured in the DCIR analysis can be mapped onto the board for thermal analysis. These board losses can have a significant impact on the temperature field in electronics devices. In the simple electronic system below, the thermal model on the left does not have losses from the board incorporated, whereas the thermal model on the right does:
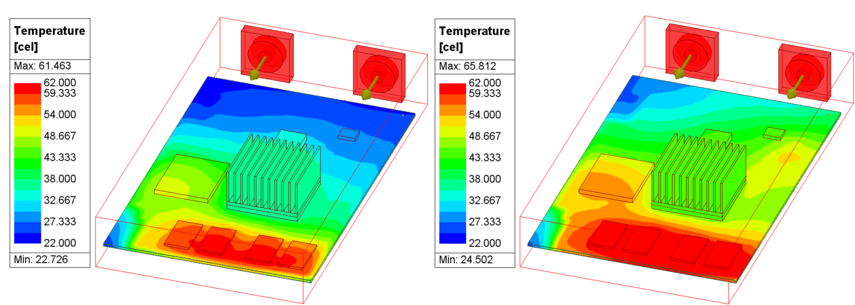
In the example above, incorporating the board losses into the thermal model provides a more accurate representation of the temperature field so an engineer can make informed decisions around cooling strategies. There is a rule of thumb often used when designing electronics with electrolytic capacitors, and that is for every increase in 10 degrees centigrade, the life of the capacitor is cut in half. This can make it crucial to include board losses in your thermal solution to provide detailed insight into how long the design will last.
Electro-Thermal Analysis of Waveguide Filter
For both military and commercial applications, waveguide filters are essential to modern radar and satellite communications. Waveguide filters with the ability to operate in a variety of challenging conditions and high-power loads are in greater demand. To better understand heat generation, distribution, and dissipation inside the waveguide structure, thermal simulation must be incorporated early in the design process.
By simulating the thermal conditions a wave guide filter will be subjected in a virtual environment, engineers can identify thermal related issues early in the design phase, implement effective cooling strategies and ensure appropriate materials are incorporated. Excessive heat buildup can cause mechanical deformation due to thermal stresses that can affect the filter’s performance and cause material degradation. Through virtual prototyping, the thermal characteristics of the wave guide filter under real world conditions can be simulated, and engineers can maintain acceptable temperature ranges which will ensure long term performance of the filter.
The electromagnetic and thermal performance of a wave guide filter can be evaluated within AEDT. Once an engineer has evaluated the electromagnetic performance of their design, the electrical losses can be converted into a thermal solution under real-word conditions. Below is an image of a thermal model that represents the waveguide filter subjected to force convection cooling to get an understanding of the temperature distribution.
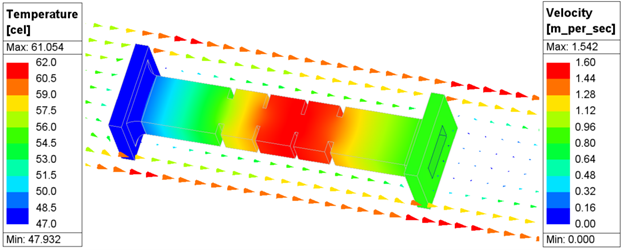
This temperature field can then be converted into thermal stress and to get an idea of how the structural will deform in the field. Studying the thermal effects of the waveguide helps engineers identify areas of high thermal stress and design the filter that ensures long-term durability and reliability.
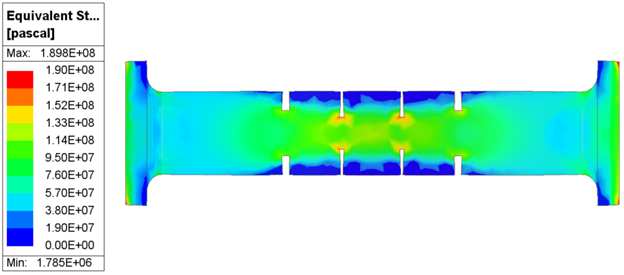
Electro-Thermal Analysis of Electric Motor
Electric motors are found throughout modern society, powering everything from household appliances to industrial machinery. They are responsible for 38.4% of the U.S. electrical energy consumption based on published information from the U.S. Department of Energy, which drives demand for new energy efficient designs. Managing the thermal aspects of these new energy efficient electric motors is often one of the most challenging aspects of the design process, and incorporating simulation early in the design process will help ensure these motors meet the high-performance requirements of modern applications.
What makes thermal management essential in electric motor design is the impact temperature can have on reliability and performance. Excessive heat can build up and degrade insulation, cause premature bearing wear, and cause demagnetization, all of which will reduce the efficiency and lifespan of the electric motor. Thermal analysis will enable engineers to explore various cooling techniques and configurations in a virtual environment to quickly improve thermal management systems and bring products to market faster.
Ansys has electrical and thermal solutions for electrical motors. An engineer can evaluate the performance of their design withing AEDT, and once the performance of the electric motor has been evaluated and deemed appropriate for the application, the losses can be converted into a thermal solution. The stator of an electric motor is often where most of the heat is generated, and these losses can accurately be accounted for. In the image below the losses in the stator are mapped over into a tool called Ansys Fluent.
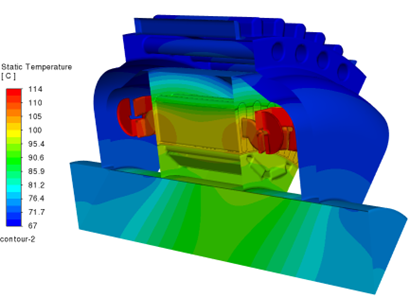
Conclusion
Thermal analysis is a fundamental component of electronics design that enables engineers to maximize efficiency, reliability, and performance by providing insight into the thermal behavior of the electrical system. By incorporating thermal analysis early in the design process, engineers can proactively handle thermal challenges, reduce design risk, and produce reliable, high-quality devices that satisfy changing market demands. In today’s competitive landscape, adopting thermal analysis as a core component of the design process is not only advantageous, but necessary for success.