Introduction
Ansys EMC Plus is a tool for electromagnetic compatibility (EMC) and interference (EMI) analysis of heavy industrial vehicles and platforms. These vehicles must meet EMI/EMC requirements to ensure safety, reliability, and performance in harsh environments. Understanding whether a device will pass or fail an EMC test early in the product development cycle is essential to reducing cost and delays. However, most electromagnetic tools are not designed for full platforms and their cables, which can have complex geometries and interactions. Ansys EMC Plus, however, is designed for this purpose. It uses a hybrid approach that combines three solvers to solve the full platform model, including the 3D fields, the cables, and the nonlinear circuits. In this document, we will briefly introduce the tool and its features, and highlight some of the new capabilities in the 2024 R1 release that are relevant to heavy industry.
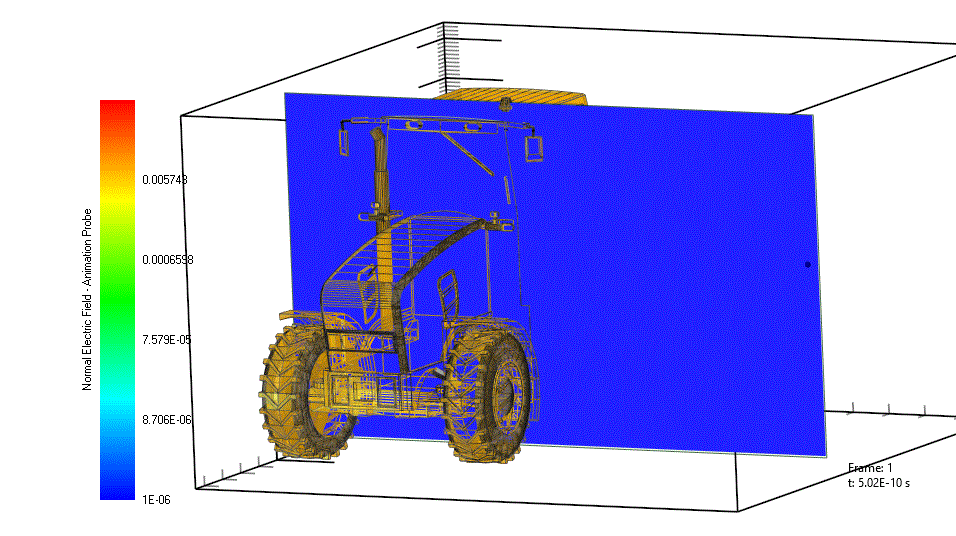
Figure 1. Simulation of Radiated Emissions from a Full Vehicle Saves Cost and Risk
Ansys EMC Plus Overview
Ansys EMC Plus is a tool that enables engineers to perform EMI/EMC analysis of heavy industrial vehicles and platforms, such as trucks, buses, trains, ships, aircraft, and satellites. The tool can handle large and complex models with millions of mesh cells and thousands of cable segments and provides accurate and fast results. The tool can also simulate various EMC tests, such as radiated emissions, radiated immunity, conducted emissions, and conducted immunity, and help engineers identify and mitigate potential EMC problems.
Ansys EMC Plus uses a hybrid approach that combines three solvers that operate simultaneously to solve the full platform model. The three solvers are:
- The 3D fields are solved with the finite difference time domain (FDTD) method. This method uses a grid-based mesh engine that is forgiving enough to be used with mechanical CAD geometry, without requiring extensive simplification or cleanup. The FDTD method can capture the complex interactions between the 3D fields and the platform, and account for the effects of shielding, apertures, and slots.
- The cables are solved with a modified multiconductor transmission line (MTL) theory solver that allows for all the cables on the platform, up to many thousands of segments, with a reasonable amount of analyst time. The MTL solver can model the effects of cable routing, twisting, bending, branching, and termination, and account for the coupling between the cables and the 3D fields.
- Finally, the ends of the cables may be solved with a transient nonlinear circuit (TNC) solver. The TNC solver can model the nonlinear behavior of electronic components, such as diodes, transistors, and integrated circuits, and account for the effects of voltage and current sources, loads, and switches.
The hybrid approach of Ansys EMC Plus enables engineers to perform EMI/EMC analysis of full platforms and their cables with high accuracy and efficiency, and to evaluate the performance of the devices under various EMC scenarios.
New Features in 2024 R1 Release
Ansys EMC Plus has new features in its 2024 R1 release that are relevant to heavy industry. These features include a new capability to automatically merge the 3D CAD geometry and the cable database information. Most manufacturers track the path of cables in 3D CAD, while the wiring diagram is stored in cable database software. Ansys EMC Plus can now automatically import and merge these disparate sources of data and create a consistent and complete model for EMI/EMC analysis. This feature can save time and reduce errors in the model creation process.
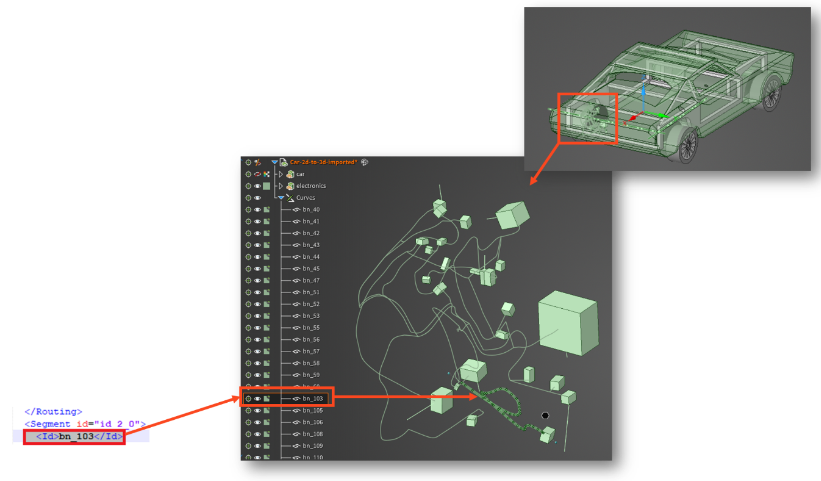
Figure 2. New Feature Allows Merging 3D Cable Paths from CAD with Wiring Assignments from Cable Database Software
A new GPU solver that increases the simulation speed dramatically. The GPU solver can leverage the parallel computing power of graphics processing units (GPUs) to accelerate the FDTD method. The GPU solver is about 12 times faster than the previous CPU version, making the tool even easier to use for complex geometry. The GPU solver can also handle larger models with more mesh cells and provide more detailed results.
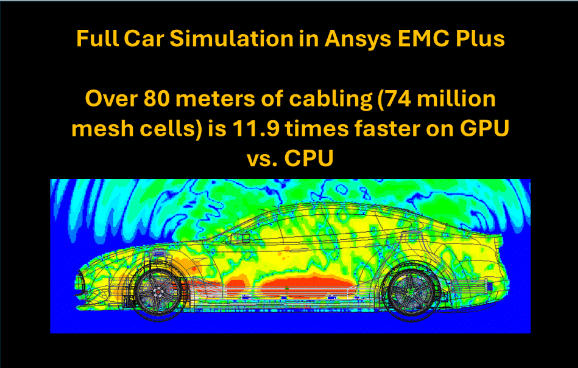
Figure 3. EMC Plus GPU Solver is Almost 12 Times Faster than the Previous CPU Version
These new features of Ansys EMC Plus can help engineers in heavy industry to perform EMI/EMC analysis of their vehicles and platforms more efficiently and effectively, and to ensure compliance with the EMC standards and regulations.
The fastest time-to-value for complex device and platform EMI/EMC simulation.
Ansys EMC Plus features a forgiving mesh and hybrid sub-cell solvers that allow for extreme geometric complexity without extreme user effort to clean and prepare geometry for simulation. Ansys EMC Plus also has a fast and intuitive user-interface that includes automated workflows and wizards to help inexperienced users become productive quickly. Ansys EMC Plus can import and merge 3D CAD geometry and cable database information automatically and create a consistent and complete model for EMI/EMC analysis. Ansys EMC Plus can also leverage the parallel computing power of GPUs to accelerate the simulation speed dramatically and provide more detailed results for larger models.
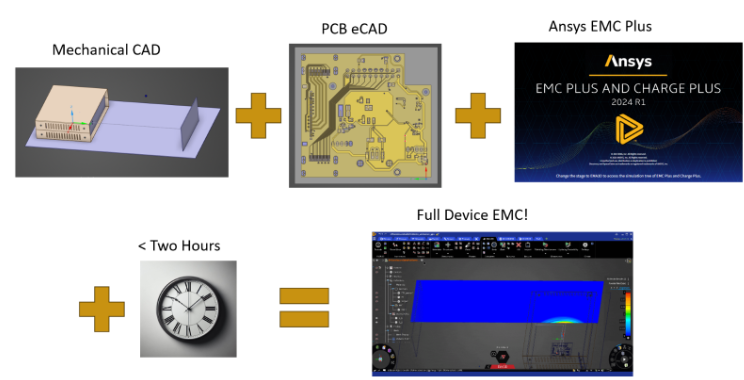
Figure 4. EMC Plus Has a Short Time-to-Value by Making Analysis Fast and Easy to Learn
EMC Plus is a useful addition to testing programs. Ansys EMC Plus can simulate various EMI/EMC tests, such as radiated emissions, radiated immunity, conducted emissions, conducted immunity, bulk current injection, transient immunity, etc. Ansys EMC Plus can also model the effects of different environments, such as ground planes, reverberation chamber, anechoic chamber, etc. Ansys EMC Plus can generate reports and plots that compare the simulation results with the standards and regulations and identify the sources and paths of EMI problems. Ansys EMC Plus can also perform parametric studies and design optimization to improve the EMI/EMC performance of the device or platform.
EMC Plus provides seamless integrations with other Ansys tools and third-party software. Ansys EMC Plus can import and export data in various formats, such as STL, STEP, IGES, XLS, CSV, etc. Ansys EMC Plus can also interface with other Ansys tools, such Ansys HFSS, Ansys SIwave, or Ansys Material Intelligence, to perform multi-domain analysis of the device or platform. Ansys EMC Plus can also work Ansys optiSLang or with third-party software, such as MATLAB or Python, to perform custom scripting and automation of the simulation process.
With these features and benefits, Ansys EMC Plus can help engineers in heavy industry to perform EMI/EMC analysis of their devices and platforms more efficiently and effectively, and to ensure compliance with the EMI/EMC standards and regulations. Ansys EMC Plus can also help engineers to reduce the cost and time of physical testing and prototyping, and to enhance the quality and reliability of their products.